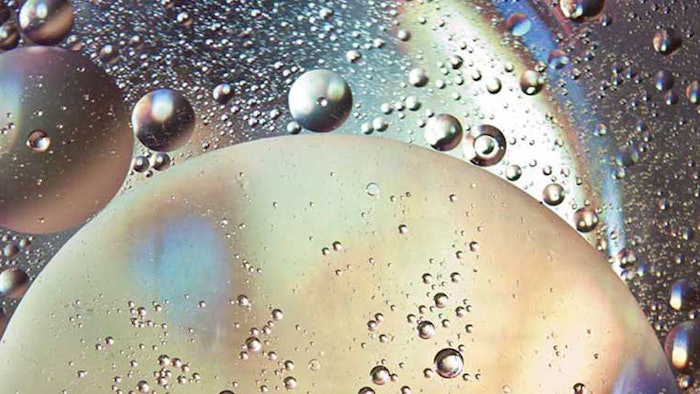
Besides directing cosmetic beginners to read the abundant literature in the field of stability, the aim of this article is to give some clues for starting stability matters “with the right foot”—indeed, to anticipate stability problems helps to speed up the R&D process.
Log in to view the full article
Besides directing cosmetic beginners to read the abundant literature in the field of stability, the aim of this article is to give some clues for starting stability matters “with the right foot”—indeed, to anticipate stability problems helps to speed up the R&D process.
In formulation, it makes good sense to say, “Quality should be created, not checked.” We can apply this rule to stability parameters but first, let’s define stability. Interpreting European law, one can surmise that stability is the continuity of functionality and safety of a cosmetic formula.
According to this interpretation, elements involved in the microbiological and chemical stability of the ingredient blend must be controlled. Thus, if ingredients maintain the same structure they had upon assembly, formula functionality and safety are guaranteed.
A slightly more extended interpretation of stability, borrowed from the pharmaceutical field, binds this concept to the continuity of product quality. According to Oxford Biosciences,1 stability means to ensure that the product maintains its intended physical, chemical and microbiological quality, as well as functionality and aesthetics, when stored under appropriate conditions.
This same concept is comprehensively described in the Personal Care Products Council (PCPC, formerly CTFA) and Cosmetics Europe Guidelines2 but “everything flows as a river,” the Greek Heraklitus once wrote. Indeed, what would be the judgement criteria for accepting or rejecting possibly unavoidable variations in properties? This question strictly relates to the specificity of each formula.
The second concern is how to build and validate evaluation models for adequately stressing, during a defined period, the samples. This means establishing the energy supplied, manufacturing details, temperature and all conditions mimicking the future shelf life and usage path.
The third hurdle is how to minimize the complexity and duration of stability testing procedures while at the same time maximizing the confidence level of results. Moreover, stability evaluations of a formula dramatically extend the development time and intricacy of a launch into the market.
Microbiological Stability
Building microbial stability in a formula is mainly achieved3 by reducing its water activity, selecting the right preservation system and keeping the emulsion and pH value stable. During development phases, the evident stability behavior of formulas prepared without excessive hygiene precautions in the short term gives important info about their ease of contamination.4, 5
Moreover, it is necessary to consider how the ingredients and packaging will potentially interact with preservatives; for example, poly-ethoxylated emulsifiers or polar polymers frequently deactivate preservatives. Also, nutrient-rich raw materials, e.g., honey and hydrolyzed proteins, should be examined not only for their microbial count, but also for their spore content and role in supporting microbial growth in the product.
On the other hand, formulae that technically cannot be microbiologically polluted, e.g., anhydrous formulae, those containing more than 20% ethyl alcohol and those with extreme pH values or very high ion concentrations, should not be tested. Microbial testing means reproducing scenarios that occur during manufacturing; e.g., contamination by ingredients, surfaces and packaging materials or wrong handling and improper filling. Indeed, most risks are caused by consumers who pick up and spread the product with their contaminated hands, exposing the surface of the product to environmental microbial charge.
The microbial challenge test is currently considered the best way to verify, a posteriori, the robustness of a formula to microbial insults. In effect, it indicates the capability of a freshly made formula to resist heavy attacks. To quickly acquire a wider confidence level for microbial safety, one can evaluate formulas containing 1/3 less preservative than the standard formula in parallel.
Another quick stress test is to challenge a formula that contains 10% to 20% extra water.6 This models of what could happen in the case where water evaporates from the product bulk and successively condenses onto its surface.
Furthermore, long-term microbial resistance should be checked over time, even if the product is already in the market. The best model is to prepare samples in their final packaging, filled only 20% and kept at room temperature for one year. Some companies carry out analytical determinations of preservatives after long storage times, but this is certainly not the cheapest way of testing for antimicrobial stability.
Chemical and Physical Stability
Again, one should not wait for the completion of the final formula before starting any stability testing. It is useful to have previously evaluated the organoleptic and physico-chemical variables of the first prototypes throughout the development process and to take note of all problems encountered; such as incompatibility, lack of homogeneity of the bulk, etc.
Keeping such records allows for the identification of possible reactions among ingredients. In general, it is useful to start preparing the base formula without the most problematic ingredients, e.g., perfumes, colors, vegetal extracts and insoluble (or barely soluble) actives., in order to identify the stability of the base alone.
Systematically adding the accompanying ingredients, one by one, makes it easy to identify those influencing stability. In the formulation steps from one prototype to the next, it is also better to modify one ingredient at a time, again to help identifying the problematic materials.
In a sunscreen containing dissolved organic (i.e., “chemical”) filters in the oil phase, one should test its cold stability by maintaining it at 4°C for 24 hr, then checking for the precipitation of crystals.
A general rule of the thumb is to assess the preliminary formula ingredient by ingredient, to identify those that could dramatically influence the behavior of the formula if they are even modestly varied. Examples include acids or alkali, thickeners and emulsifiers. Building models whereby variations are purportedly obtained, one by one, and verifying their behavior over a short period, e.g., one month, can paint an interesting overall picture of stability behavior.
In order to reproduce the chemical storms that can happen during shelf life and identify the formula’s stability profile, some classic test models can be used to overwork samples, described as follows.
Extreme Temperature
The most popular tests raise or lower sample temperatures to higher or lower than ambient or room temperature. Ambient is generally 25°C while higher values are 50°C, 45°C or 40°C. In general, the more extreme the condition, the more the results will rely on an expert’s evaluation.
At 50°C, many active molecules decompose, perfumes evaporate, oxidation and hydrolysis reactions take place faster and liquid crystals structures disappear. At 40°C, however, the acceleration of unwanted reactions may be too slow. An optimal testing temperature of 42°C-43°C is suggested. Logically, if a product will be marketed in hot climate, though, the 50°C test is also necessary. Moreover, in shampoo, discoloration can occur at 50°C after two weeks, whereas it takes four weeks at 43°C.
To improve the microbial safety confidence level quickly, evaluate formulas containing 1/3 less preservative than the standard in parallel.
Remember temperature indiscriminately increases the speed of all reactions, per the Arrhenius law, and that time takes the lowest activation energy to allow reactions to occur. In other words, cosmetic reactions that are heavily reliant on high temperatures are always less stable over time. Freeze-thaw cycles, even if their duration is just two or four weeks, are even more puzzling. They provide a reliable sense of a formula's behavior only when the results of several formula variants are compared. Stabilization or destabilization effects of additives are clearly observed.
For the described high-temperature tests, the suggested duration depends on the stage of the formula's development. Preliminary samples, e.g., those made in the lab and not deaerated, are kept in glass containers for three months maximum with controls each month. Pilot plant samples are kept for six months in their final container and controlled at one, two, three and six months.
The first industrial run is controlled as above, plus one control after a year, but just for samples kept at room temperature and 4°C. Samples kept at 4°C generally represent the “freshly made” formula, which is ideal for comparisons with high-temperature samples. They also indicate the behavior of the formula at a low temperature. One classic problem encountered is the precipitation of allantoin in form of sharp needles from saturated aqueous phases kept in cold weather conditions.
Combination Test
Window test: A very Empiric but instructive test is the “window test.” This literally consists of putting the samples near to a glass window exposed to the south. The day and night temperature cycle and the UVA and visible light irradiation easily challenge the formula parameters. Again, this is a good comparative test, and lasts only one month maximum.
Centrifugation: Centrifugation also is frequently carried out. In a series of experiments aimed to identify the best duration, temperature and acceleration to discriminate stable from unstable o/w emulsions, our lab identified the following conditions: 7,000 g for 30 min at 35°C with an experimental error on the order of ±10%. This is based on more than 20 years of experience.
Unfortunately, w/o emulsions and suspensions with solids cannot be tested in such a way. The advantage is the very short time necessary to get the answer. Again, answers are better when testing in a comparative mode.
Transport: Another test is to put the samples in their final packaging in the trunk of a car and drive on different days for a total of at least 2,000 km (~1,243 miles), then examine samples. The combination of vibration plus temperature cycles is challenging both for the product and the package, including inks and labels. Laboratory equipment that reproduces these conditions only gives vibrations and shaking without the effects of temperature cycles.
Chemical Analysis
Chemical analysis generally is applied to test active ingredients. For example, in the case of sunscreens, one could test UV filter content; although dealing with complex mixtures, especially with mineral filter suspensions, it is more convenient to check the UVB and UVA SPF values. To save time and money, the number of volunteers can be reduced in respect to the standard. If the new values statistically fit into the set of values obtained at time 0, then a formula's functioning and safety can be considered stable.
For detecting the oxidation stability of vegetal fats and oils, the peroxide number can be measured, while for hydrolysis resistance, the amount of free fatty acids developed can be evaluated. One instrument that is quite predictive to test the robustness of an antioxidant system is called Rancimat. It blows air into the sample at high temperatures.
While the amount of volatile compounds formed with different levels of antioxidants is indicative enough, a preliminary Empirical test for oxidation fastness is an olfactory test. Here, a thin layer of product is put onto a glass slide and in a glass jar with cap. The jar is stored at 42.5°C, then evaluated by olfaction after one week by a trained evaluator.
Physical Tests
pH values and rheology are the most common types of stability tests and they include many contemporary changes. Defining acceptable variations, in the case of pH, will depend on experience, composition, historical background of the formula and its efficacy parameters. In general, ± 0.5 units is considered acceptable when the formula is at a pH from 5.5 to 7.5. More acidic or alkaline starting values require a reduction in the acceptability interval to ± 0.2 to 0.3 units. Note that general rules do not apply to special formulas such as those containing high amounts of urea.
Methods based on emulsion turbidity7, 8 are also successful for a large percentage of emulsions, and measuring the zeta potential of emulsions9, 10 is a good way to predict long-term stability, as high values (> 25mEV) suggest the prevalence of repulsion forces among the particles.
Packaging
Weight variation in packaging materials can help to identify the absorption of ingredients from the formula. These variations are checked in samples kept under vacuum for a certain period. Tight closure effectiveness can also be verified under vacuum by filling the containers with colored liquids.11
Humidity absorption is another test that is especially good for final packaging materials. Here, samples are kept at 70% RH and 45°C. Checking the integrity and visual appearance of the packaging material is important both before and after accelerated temperature tests. Dispensing conditions and continuity are also important factors to test and control.
Sensory
Sensory or organoleptic evaluations are usually carried out by a technical “expert” in the R&D or quality assurance lab.12 Further, to maintain objectivity, one can apply standard methods of panel sensory analysis, including the duo trio, triangle or ranking test. These are especially useful to understand if rheological behavior differences are easily detected by consumers.13 Before evaluations, a correspondence scale between sensory answers and viscosity values should be developed to allow for the creation of a table having numerical values bound to imperceivable differences.
Last but not least, applying the product and spreading it over the skin is the expert’s conformity control, which is more responsive than many instrumental controls.
References
- https://oxfordbiosciences.com/stability-testing/ (Accessed Sep 16, 2016)
- PCPC (formerly CTFA) and Cosmetics Europe, Guidelines on stability testing for cosmetic products (3-2004)
- H Ziolkowsky, Industrial hygiene in the cosmetic sector, DGK Verlag für chemische industrie 122 (2010)
- W Siegert, Microbiological quality management for the production of cosmetics and detergents, SÖFW (Nov 2012)
- N Tschierske et al, Efficacy loss of antimicrobial actives in emulsions, SÖFW (Apr 2012)
- A O'Lenick, Comparatively speaking: Water content vs. water activity, Cosm & Toil (Dec 2010)
- www.alfatest.it/pagina.php?p=17 (Accessed Sep 16, 2016)
- www.lum-gmbh.com/LUMiSizer_product-information.html (Accessed Sep 16, 2016)
- Gasparelo et al, Zeta potential and particle size to predict emulsion stability, Cosm & Toil (Nov 2016)
- H Saunal, Influence of homogenization on emulsion stability, Intl J Cos Sci (Oct 1982)
- D Cadwallader, Stability testing, Cosm & Toil (Aug 2010)
- F Achim et al, Stable formulations with critical ingredients, Cosm Tech (Jan 2016)
- N Wanek, Trouble-shooting with sun protection, SÖFW (Jul 2011)